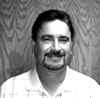 | Art Bryan
is president and owner of Southwestern Remodeling Contractors, Inc. Art started Southwestern Remodeling Contractors in 1970. Southwestern is a fully-licensed residential and commercial licensed general contractor in Wichita and the surrounding counties. Art has been a member of the Wichita Area Home Builders Association and the National Remodel Council since 1974. In mid-2000 Southwestern received the distinction of being named one of the "Top 25 Most Diversified Remodeling Companies in the United States.” Southwestern is listed as the 84th Top Remodeler in the country by Qualified Remodeling Magazine. Art can be contacted at his office at (316) 263-1239, fax at (316) 263-6230, or you can e-mail him at ARTSWR@aol. Com |
Home Improvement
2002-05-01 15:03:00
Plastic wood?
Answer: Plastic wood… these two words, until very recently, were not used in the same sentence unless you were talking about some sort of wood filler for nail holes. If you told an old carpenter that you're going to be building a plastic deck, you'd probably be laughed out of the shop. However, as the old saying goes, "times are a changing".Concerns about our environment and the effects of thousands of tons of plastic ending up in disposal sites daily have increased our awareness of this growing problem. Companies, as well as the scientific community, are looking for ways to turn this waste into a re-usable resource. Canadian Plastic Lumber (CPL) is one of those companies who use waste plastic to manufacture a product called PLASBOARD, one of the many new "alternative to wood" building products that are helping to combat this potential environmental nightmare. CPL reported that they will " turn over 2,000,000 pounds of post consumer plastic waste into plastic lumber this year. As a renovation and kitchen cabinetmaking contractor I'm always on the lookout for leading edge products. Whether or not Plasboard is one of them is yet to be seen. Recently, products such as the new wood "I" beams, house wrap materials, energy efficient widows, and innovations in kitchen cabinetmaking hardware have had an effect on how we build and design. Decking, up until a few years ago, meant using traditional wood products such as cedar, redwood or pressure treated spruce. Today more and more companies are investigating alternative products for decks, fences, and other outdoor structures. CPL believes a natural fit is all the waste plastic that we discard. The problem is how to manufacture "wood" like material that is easy to use and cost effective to manufacture. More importantly of course, is the problem of consumer acceptance of a material that will replace wood. Plasboard, according to the manufacturer's data sheet, is durable, maintenance-free, comes in a variety of colors, is guaranteed not to rot, and is skid resistant especially when wet. The product comes in gray, green, and brown presently. You will however find quite a variance in each color selection. One of the major concerns with plastic lumber is the expansion and contraction properties. Because of this, a "floating" structure has to be built on a fixed structure. The expansion and contraction rate is stated as "3% times the length of the product if temperature variations of 50 degrees centigrade are likely". Using the manufacturer's formula, and given our weather conditions, the maximum expansion and contraction of an eight foot board would be .29 inches or a little better than one quarter of an inch. Therefore a twelve foot wide deck could expand and contract about three eighths of an inch from the heat of summer to the cold of winter. Plasboard, like wood, is available in many sizes suitable for deck construction. This product can be treated like wood in many ways. You can cut it (use carbide tipped blades for best results) and drill it, but it cannot be used as a structural member. You must build your deck structure with traditional wood products. There are other special considerations when building with plastic lumber. Most important is the fact that the expansion and contraction factor has to be accounted for, particularly with deck boards. The structure supporting the deck boards must be built independent of the fixed structure. In effect, you must build a "floating structure" on the fixed supports that are anchored to the house and piers. Currently, Plasboard 1" x 6" boards are only available in eight and ten foot lengths. Building practices that many take for granted must be reviewed because of the differences and oddities of this new plastic lumber. For one thing, joists must be in a perfect plane with each other. It is important in conventional lumber deck building, but critical with plastic lumber deck building. Lumber, particularly 2 x 6's will push down or lift up on the odd joist that is slightly out of plane with the others. Plasboard, because of its flexibility, will simply ride up and down across the joists and you end up with a "wavy" deck surface. There are a few other oddities with plastic lumber that you should be aware of before building. When installing screws you must pre-drill and countersink to prevent the plastic from "puckering up". Voids in the lumber, particularly the 2 x 2's and 3 x 3's, caused by air pockets during the extrusion process will not allow you to angle cut the balusters, if you like that look, for the deck railing. Plasboard, as well as most other plastic lumber, is not structural therefore railings may not meet the building code for decks a certain height above ground level. You always want to be sure what you do is to code. To secure the deck boards, you could use an air nailer with three inch, epoxy coated, galvanized nails; or driving three-inch galvanized nails with a hammer will work just as well. You can also screw the deck boards down as an alternative however, it would take you a while to complete this method as each hole must be pre-drilled. Be prepared for a pretty good strike with the hammer and punch to set the nails below the deck board surface. One good note is that the gap between the boards will not change, as plastic lumber does not suffer from moisture loss and shrinkage. How does this product compare with traditional wood like cedar or pressure treated lumber? The cost, including railing and stairs, is approximately $7.20 per square foot. It's higher than pressure treated lumber but certainly comparable with cedar. Subtract the cost of finishing and you've got a competitive building product option. I have heard however, that a 15 to 20% increase in the cost of Plasboard is on the horizon. This means that the cost would rise to about $8.00 per square foot. Remember that the costs given are for materials only. Labor costs will have to be added if you plan to have someone build your deck. There are a few disadvantages that must be accounted for when deciding if this material is right for your deck. Product length is a maximum ten feet, air pockets and voids may force you to alter your design, color consistency from board to board varies somewhat, and streaking caused by poor mixing of some types of plastic must be considered. However, when you weigh the disadvantages against the fact that you end up with a maintenance- free deck that never needs painting and will not rot, Plasboard could be a good alternative. Being a traditional remodeler, I think we might still be quite a ways away from using products like Plasboard on a wide scale.